Introduction: The Fabrication Assistant
I really can't recall the numbers of times I'v been trying to build something and needed a part to just stay put so that I could figure out how to deal with it. This usually requires it to float in mid air while I work out structure to go from it to the existing parts of the project. Last year I told myself I'd had enough, it was time to stop putting off planning a holding arm and *just build it*
As such, although I will share specifics of the build of this project, try to see past them. This project was built with scrap materials, problems were figured out on the spot. If your going to build it, your materials will be different, this project can serve as a suggested path. Many of the build methods here are the same, I will attempt to detail each one for the first time their used.
*Personally* I can ad-hock a project MUCH more successfully than planning it to death. The trick is to be fearless, if something doesn't work, change it!
Some general goals:
- Be able to hold up to a 10lb load
- Have a reach of 24" from the base.
- Be EXTREMELY positionable.
- Be 'Technology-free' no microcontrollers, electronics, motors, something that just works. ;-)
- Be weatherproof, I don't have space for all this stuff in my shop!
One of the really fun things about this project is that it holds itself in place while your building it. Its its own first project!
Supplies
- welder & friends (angle grinder, goggles, band-aids, etc)
- lathe
- 3d printer
- supply of various sizes of pipe
- 4 door hinges
- 1/4" nuts
- 1-1/2" x 1/4" bolts
- 1/4" bar
- 1.5" angle iron
- snazzy paint.
Step 1: Starting the Base.
To suit uneven ground, I'm going to go with a tripod type base. As part of "make anything with a welder" I'm going to use hinges I bought at a second hand store for $1.50ea.
Materials:
- (x3) 4 inch door hinges
- 3 pieces of 1.5" angle iron 19" long
- 1 upright pipe (ID 44.7mm OD 48.5mm (its some sort of thin-wall, 1.5 inch pipe) length 21.5 inches)
- Weld 3 hinges into a triangle. Each of the outer flaps will hold a leg, the union of the inner flaps will support the main upright pipe segment.
- From each of these, comes a leg, I'm using 1.5" angle iron from the pile of bedframes. (bedframe metal is fine up until you need to drill a hole in it, so make sure any holes needed can be welded on) Each of these legs is 19" long.
- From the center of the overlapped hinges, comes off the main support shaft. I'm using a larger size pipe, I will be slipping a smaller pipe down into it to achieve rotation.
I'm going to cover the lock details in the next step, as there are 5 of them on the project, but its just the same thing over and over.
Step 2: Building Axis Locks.
In total, this project uses 5 of these locks, but 9 of the handles, and 6 collars for them.
Handles (x9):
- Cut a 3" piece of 1/4" round bar.
- Weld the bar to a 1.5" x 1/4" hex head bolt.
Your challenge is to get it centered on the bar AND the head of the bolt at the same time. I think I got one right, the rest inhibit me sleeping at night.
Lock collar (x6 (one of these is used on the wrist)):
- Drill a 13/64 hole into the side face of a 5/8-11 nut
- Tap hole to 1/4-20
Tab assembly (x10) (half these get attached to the frame):
- (x2) Cut a piece of 1/8inch thick steel to 3/4 inch x 1.5 inch
- Drill a 1/4" hole in it towards one end, such that there is only a little more than 1/8" of metal between the hole end the end-edge of the tab. (for 1/4" bolt)
- Using 1/4"-20 x 1 inch bolts, fasten two tabs together, pointed away from each other. Use two nuts, lightly lock them together (so that they can be forcibly turned) (this assembly will be easier to handle than just the tabs themselves. We will unlock them later.)
The locks are different sizes depending on where they go and the range they need to span. I will specify the sizes I used for the spike/pipe as they are used in the project.
For each lock you need:
- Large spike (12 inch, 3/8" dia) I use galvanized (hair larger than 3/8") for weather protection.
- Lamp pipe (ID 0.5inch OD 0.4inch)
- Tab assembly (as above) (x2)
- Handle (as above)
- Lock collar (as above)
- File the knurling off just below the head of the spike, it moofs up things 'casue it doesn't fit into the lamp pipe.
- Weld a tab assembly to the head of the spike. (my apologies, on the photo, I'd apparently ditched the head on the spike)
- Drill a 9/32 hole in one end of the pipe
- Weld a tab assembly to the *other* end of the pipe from step 3. (I sealed off the end of the pipe and centered the tab via welding as I did this, but you CAN weld the tab to the side of the pipe, although, it does not provide any advantages to operation) make sure the face of the tab is lined up with the hole drilled in the other end.
- Screw a handle into a lock collar so that it does not protrude past the inside
- Fit the lock collar over the end of the pipe with the hole, thread in the handle so that it goes thru the drilled hole. leave it just tight enough to stay put while your about to. (Yes, the nut is loose on the pipe, won't be after next step)
- Weld the lock collar to the pipe. (easy now, that metal on the pipe is thin, focus on the collar, make a pool, and once you have it, coherse it into the pipe metal and as soon as its there, THEN STOP AND RUN AWAY. It might be all sparks and flames and sound and light, but its all happening quite slowly) These only need to be a small weld, they are not taking stress, they simply pinch the pipe and spike together.
- Undo the lock handle, slide in the spike, and gently lock (with the tightening already).
After these are attached to the frame, remember to back the nuts off a tiny bit and lock the two of them together (tighten against each other)
Step 3: Adding Locks for the Base.
The locks are tricky. You need to make sure that, for the position range they can provide, you get the angular range you need on the joint their connected to. The locks need to have as much leverage on the joint their locking as you can give them, these end up with LOTS of force on them, more leverage will help their lives.
The range of a lock is not the point where the handle can't grab the spike, but the limit where the spike is held enough to not slip out sideways (buckle).
You can play with it, I'v used the following for my base locks (after lots of trial and error):
- Pipe length: 8-1/4 inches
- Spike length: 9-1/4 inches (top of head to tip)
- Attachment distance from hinge pivot to leg: 7-1/4 inches
- Attachment distance from hinge pivot to upright: 9-3/4 inches
Attach locks: (x3)
- Measure off / mark positions for tab connection point of locks
- You can hold the whole assembly while welding the first bit, weld the yet-unused tab (pipe end. This will keep rain out of the pipe) of the lock to the upright (just tack it on)
- Force the other locks ends tab as required to weld it to the leg, again, only tack it.
- Back off the lock handle and test the range of the leg. Moving the tabs away from the hinge point will utilize more range on the lock, and reduce its mechanical stress. Moving the hinge point towards one end of the lock will increase the range of movement the lock covers. I have set these locks as I did, so that I can lock the legs *almost* straight down, but only up to 90 degrees from the upright (as that would sit the whole assembly right on the ground)
- When happy, finish the welding on the tabs.
Step 4: Upper Base
While going thru my supply of pipe, I found two sizes I liked for rotating joints. I had enough supply to cover all the joints, meaning I could repeat the same process for them. Each rotating joint is made from 2 sizes of pipe that have enough clearance between them to be able to fit a 3d printed bushing (PLA is really good at wear(6/10) and compressive loads(9/10)) The smaller of the pipes is able to fit a 1 inch nut modified as a retainer ring. Pipe intersections are done via a piece of angle iron. One face of the angle iron welded to the end of the pipe, and the other pipe welded into the mouth of the angle iron.
I have a piece in here that I turned on the lathe, I would have 3d printed it, but all 4 printers were busy making the other bushings.
My larger pipe is ID: 44.7mm OD:48.5mm
My smaller pipe is OD:34mm (1" schedule 40 steel)
See drawing for turned bushing.
- 2.5 inch piece of larger pipe.
- 12 inch piece of smaller pipe.
- 2-1/4 inch piece of 1.5" angle iron.
- 1x 3d printed deep bushing. (thingiverse # 3834029)
- turned bushing
- #10 machine screw.
- 2.5" length of 1/2 inch round bar
- big washer ID:35+-1mm OD:58mm+-6mm
- The big pipe needs to be a clean cut, I'v taken this piece to my lathe to square up the ends.
- Weld large pipe into the V of angle iron, centered.
- Weld result of step 2 to end of the small pipe.
- Wait/cool everything off.
- Drill a 1/2 inch hole in the small pipe 3/4" down from the angle iron. (This will be a pin for the small pipe to sit on, meaning the weld doesn't have to be nice to the bushing under it.)
- Insert the 1/2 inch bar thru the small pipe (if everything went well, the hole is a bit small, and you need to tap the bar in with a hammer, less, a *small* tack weld on the top side of the bar will hold it, we already installed the other bushings so you don't want to heat it up now.)
- Insert washer on small pipe
- Insert 3d printed deep bushing on pipe
- Insert turned bushing on pipe. This bushing will go at the end of the small pipe, the hole drilled in it is meant to fit the head of the machine screw.
- Mark the position of the hole in the machined bushing onto the small pipe, remove bushing.
- Drill marked with 5/32 and thread with #10 tap
- Reinstall bushing, align holes, Install machine screw and tighten. (At this point you have a one-go assembly. That upper bushing can't really be taken apart easily if this doesn’t work)
- Hold this assembly against the current base with the upper bushing at the top of the upright, in the way it will all slide together. Mark a position about 1" above the top of the lower (machined) bushing on the base upright. (The lower bushing is a 2 part deal, it nonally keeps the smaller pipe centered in the base, the lock were about to install on that mark retains it vertically.
- In the base upright, drill a 9/32 inch hole.
- Spin a 1/4" nut onto a lock handle
- Set the nut and lock handle into the drilled hole, and weld. (careful not to: Get weld splatter on the lock handles threads, Weld the lock handle to the nut/base/anything) This does need a pretty complete weld as its pressing the lock handle into the smaller pipe of the other assembly we just made.
- Unscrew the lock handle (right out is fine)
- Make sure the upright pipe on the base has cooled off.
- Give the machined bushing some grease
- Slide small-pipe assembly into base. (The turned bushing should slip right in, the 3d printed bushing will take some force to fit onto the large pipe, this is intentional, it may even shave a bit off the 3d printed bushing, using a soft mallet to seat it is fine.
- Lightly tighten rotation lock handle back into base
Hey! thats the base done! Now were onto "arm" segments.
Step 5: First Arm Segment
This next segment will have a going-forward end just like the top of the base. The main detail here will be the part of the hinge that meets that pipe on the base. This joint was a prototype for what I'd like to use on my 12' mecha :-)
- (3x) large pipe segments
- (8x) 3d printed bushings (thingiverse # 3834029)
- 1.5" angle iron (5.5 inches long) ("large span")
- (2x) 1.5" angle iron, (1 inch long) (spacers)
- 1.5" angle iron, (2 inches long) ("short span")
- segment pipe (34 inches long)
- Interface piece (I used a piece of shallow unistrut, you can use some 1.5" angle iron if you want)
- hinge pin pipe (OD: 29.8mm 1" EMT)
- (2x) huge nuts (1 inch, 8 tip)
- (2x) 6-32 screws
- axis lock (spike:8 inches, pipe: 3.5 inches)
Hinge pin retainers (x2): (there will be 6 of these in total for the project)
- Bore large nut to 30mm
- Drill 7/64 hole in side face
- Tap to 6-32
Segment:
- To the inside of the "large span" piece of angle iron, clamp the spacer segments of angle iron, these need to be seated rather well as they ARE our alignment for this joint.
- Weld on the edges, not on the ends, make sure that the inside of the spacers don't have bumps, we need to sit the pipe segments in there without pointing them wrong.
- Clamp a large pipe segment into one of the spacers, centered, weld into position.
- Form a notch in the "large span" angle to fit over the angle iron used on the base. (1/2 inch deep by 2-3/4 inches long) (angle grinder)
- Wait/assist it to cool.
- Grab 2 of the 3d printed bushings, mock up (via the shoulders on the 3d prints) the assembly to determine where the second large pipe needs to be welded to the second spacer, where ever it is, give it just a *hair* more room, clamp big pipe into position against spacer.
- Weld 2nd pipe into position.
- See image for orientation. In the middle of the long span, weld the Interface piece for the main segment pipe. The face choice of this will be important, I know cause I got it backwards on my first go. The two pieces of angle iron that interface with the hinge pipe segments will get in the way of each other and limit the motion if you use the wrong edges.
- Weld on the main segment pipe. I welded this 22 inches from the end of the pipe (hinge-pin-pipe end to unistrut center), the overhang is an opportunity to attach a counterbalance, and, as it turns out, is a perfect carrying handle.
- Weld the "short span" piece of angle iron to the middle of the 3rd piece of large pipe.
- Weld the face of that piece of angle iron to the end of the segment pipe, align the big pipes as best you can, mine came out a few degrees twisted, its one of those things that keeps me awake at night.
- Again with the metal cooling.
- Press in the 3d printed bushings (x6). There is a trick to the double end, place the printed bushing on the inside of the pipe, side in the hinge-pipe thru the opposite side, but place a block of wood between the end of it and the bushing. you can then push/tap in the bushing.
- Weld the spike end of the axis lock to the angle iron on the bases hinge (see photo)
- Wait/cool metals
- Insert the 3d printed bushings (x2) for the larger pipe of the base. I used an arbor press for this, Its meant to be tight, the 3d print might have a bit shaved off it in the process. If your using a hammer to set it on, buffer it with a piece of wood (2x4) and make sure its straight all the way down. You can also use threaded rod and some large washers to just "squeeze" it all together.
- Install assembly on base, push hinge pin thru everything, should go pretty easily.
- Install a pin retainer on each end, use 6-32 screws to lock into position.
- Weld axis lock to arm segment. ( 11 inches from pin to arm segment (measured to pivot bolt))
Step 6: Second Arm Segment
The major difference between this and the last segment is the ability for it to twist. The twist is done the same as a hinge in the last segment.
- 1.5" angle iron 6 inches long "long span"
- (2x) 1.5" angle iron 1 inch long "spacers"
- tipper bar 2 inch piece of spike cut-off
- interface piece (shallow unistrut) (2-1/4 inches long)
- large segment pipe (22 inches long)
- small segment pipe (29.5 inches long)
- large hinge pipes (1-3/4 inches long)
- (6x) 3d printing bushings
- (4x) retainers (based on 1 inch nut)
- hinge pin (pipe OD:29.8mm (1" EMT) 9-1/4 inches long)
- axis lock (spike 7-3/4 inches, pipe 7 inches)
- 4 inch door hinge
- plate for lock bar (1/8" steel plate, 1-1/4 inch x 2-3/4 inch)
- hooked lock bar (1/4" hook bent, dia. 5.5 inches)
- Nut for lock bar (5/8-11) (the 6th slider lock nut)
- lock handle.
Rotation lock nut: (this is the same as the slider locks)
- Drill 13/64 inch hole in face of nut
- Tap 1/4" threads.
Segment:
- Weld spacer angle pieces into "long span" piece
- Weld on one of the large hinge pipes
- The long span needs to be notched out (1 inch x 3 inches) to accommodate angle iron on other side of hinge assembly, see images!
- Mock/Space/clamp/Weld the second pipe (same as before)
- The interface piece for this needs to be tipped by 17 degrees back to allow a proper range of movement. in order to weld it there, the "tipper bar" is welded in between them. (see picture)
- Weld the large pipe segment to the interface (15.5 inches from wrist end to center of unistrut (interface))
- Install the 3d printed bushings into the hinge pipes.
- Assemble this segment to last segment. Install the hinge pin ( pipe), lock with 2 retainers (1 inch nut based)
- Install the axis lock (2-3/4 inches on the first segment, 13.5 inches on the second segment)
- Install the 3d printed bushings into the segment pipe.
- Install bushings in large segment pipe.
- Drill 9/32 inch hole in side of large pipe segment for rotation lock. (about the middle is fine)
- Install rotation lock, same as rotation lock on base upright.
- Slide small segment pipe into large segment, lock in place with 2 retainers (big nut based)
- Cut slot in one end of the small segment pipe, suitable to fit the door hinge ( I used a cutting disc)
- weld door hinge into end of small pipe.
- weld lock plate to hinge (see images)
- weld lock bar to lock plate, make sure the center of the curve to the lock bar is centered on the hinges pin, and the bar stays at a fixed distance from the small segment pipe when rotated (I drew a line on the segment to help me)).
- Slide the lock nut over the lock bar, weld the lock nut to the small segment pipe, shim as required to make sure the bar is centered in the nut, shim the weld as required.
Step 7: Wrist
The idea is that this be as universal is possible, I wanted it to be able to hold round and flat things just as well. I concluded that the best way of doing this was to NOT put on a classic gripper, but to provide a 'bar' that I could clamp things to.
- Spike (were gonna use its head end as a retainer)
- 5/8 inch x 5.5 inch bolt, with threads cut off (3.5 inches after cut)
- 1 inch bar, 3.5 inches long.
- Washer ( 1/4 thick with OD 1-3/4")
- lock handle.
- 1/8" steel plate (1-1/4 inches x 1-1/4 inches) (pin backing)
- 1.5" angle iron, 4 inches long. (this is for attachment interface)
- Cut head of spike off at 1-1/4 inches(including head), this will be a retainer for the wrist.
- Weld pin backer plate to hinge. This should be set back so that the bolt being used as a pin, has its head fully behind the edge of the hinge.
- Weld bolt (pin) to backer plate. Make sure not to get weld/splatter beyond the bottom of the head of the bolt, we need that to be smooth.
- Centered, weld the washer to the bar, This was actually something I had pre-assembled in my scrap bin. We want the washer to be as straight and centered as possible. I took what I had to the lathe to clean it up. Focus welding not on the inside of the washer/end of the bar, but around the edges where the pin meets the washer.
- Bore out bar. I used my lathe to bore a 5/8 (its going to fit on the 5/8" bolt, we want it to rotate freely) inch hole down the middle. It does NOT have to go all the way thru, just deep enough so that the washer sits up against the hinge when placed on the pin.
- Drill/thread a 1/4"-20 hole in the side of the bar for the lock handle.
- Grease up the pin, slide bar onto it, lightly lock via handle.
- weld the shortened head of the spike to the hinge, reaching over the washer and retaining it on the pin, but give it some extra space (1/16" or so)
- Cut notch in angle iron (see images)
- weld angle iron to bar. (yes, the grease will hate you)
Step 8: Paint
Hey, its NOT just about looking like something other than a pile of scrap metal scabbed together with ugly welds. its about protection from the elements!
And hey, in the line of work this thing will be doing, its going to get LOTS of scratches, splatters, and bumps, so there will be more coats to come, so don't get too crazy about quality!
- Base coat. Paint the whole thing white, don't be picky. Funny thing about paint, even a really thick coat, applied to material of different tones, comes out different.
- Wait for paint to dry
- For mine, I wanted some orange Daffy duck rings, I hit all the areas I wanted to have colour with paint, (no masking, just sloppy, cause my overcoat is black)
- Wait for paint to dry
- Apply masking tape to areas you want to RETAIN colour
- Paint the whole thing with the overcoat, in my case flat black.
- Wait for paint to dry.
- Remove masking.
I separately masked and painted the lock handles yellow too.
Step 9: Write an Instructable!
You probably made improvements and stuff, I want to see!
How did you paint it? Did you swap out that whole complex hinge thing I did for just *hinges*?
Did you motorize it? hydraulics? Pneumatics?
If not a whole HOWTO on building it, at least post a photo journal of your build, cmon!
Find me, tell me, Via instructables, I'm also on IRC and twitter.
And just maybe, if your lucky, it will win you some funds to buy you that graphite smelting pot you need for doing aluminum casting cause the one you made out stainless steel springs a leak like EVERY SINGLE TIME YOU USE IT!
Keep 'makin!
Rue
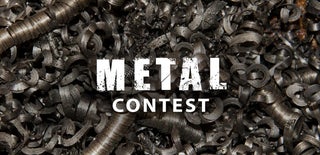
Participated in the
Metal Contest